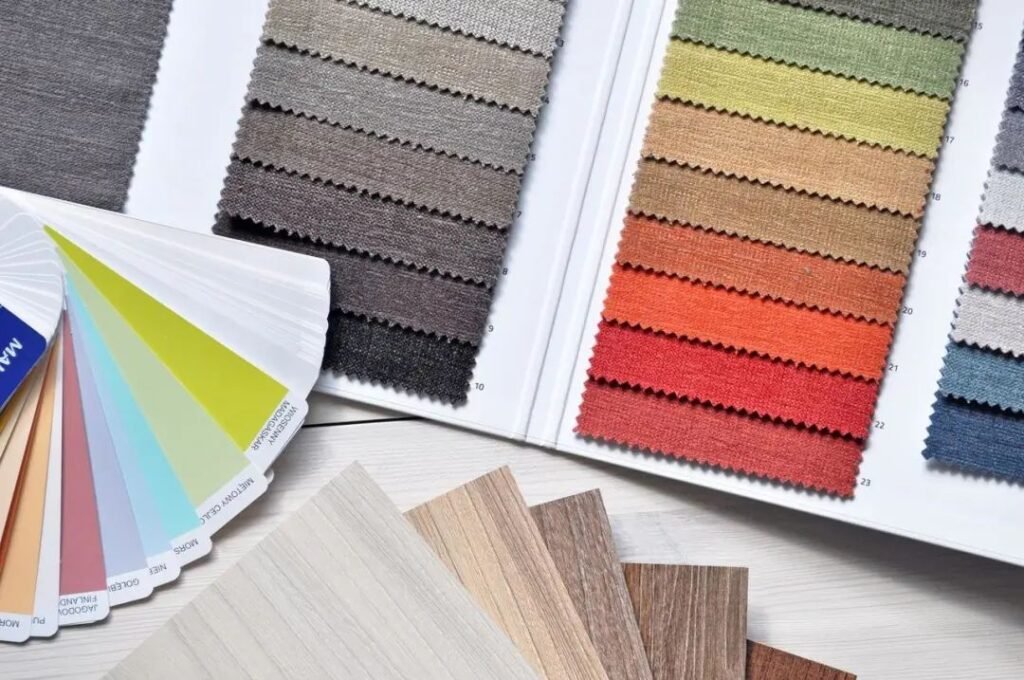
1. Pay attention to customer requirements before receiving orders
Textile fabric printing and dyeing there are several matters must not be vague, including the color light source, environmental protection requirements, door width and classification, gram weight, shrinkage rate and weft deviation, color fastness, feel quality, color difference, PH value, loss and special finishing, some chemical or physical indicators must not exceed the scope, these are international standards to restrict, printing and dyeing fabric factory must not be careless. Fabric printing and dyeing should pay attention to matters and simple index standards.
1.Color light source.
The color of the fabric under different light sources is not the same, so before the textile fabric is colored or put into production, the supply and demand sides must unify the color of the light source, so that everyone’s standards can be unified. The main light source is ① natural light ②D65 ③TL84 ④U30 ⑤ fluorescent lamp ⑥CWF.
2.Environmental protection requirements.
Environmental protection is a requirement for the inherent quality of textile fabrics, with the continuous improvement of human health awareness, do not meet the environmental standards of dyestuffs are basically absolutely eliminated, so fabric factories to enhance environmental awareness, understand international standards and strictly implement. The environmental protection standards of textile fabric printing and dyeing are as follows: ① azo does not exceed 10mg/kg; Formaldehyde, skin contact less than 20mg/kg; ③ Aromatic amine 0.2mg/kg outerwear is less than 75mg/kg, decorative material is less than 300mg/kg; ④ Heavy metal does not exceed 0.02mg/kg.
3.Door width and classification.
Although there is no unified international standard for the fabric door width, there are some common conventions in the industry, under the premise of machinery and equipment permission, some customers in order to avoid cutting waste to save costs, will require the fabric factory to supply according to a certain width.
4.Gram weight of fabric.
Gram weight is the thickness index of textile fabrics, and it is also a standard reference to prevent fabric factories from cutting corners. The error between the gram weight of the general fabric and the standard sample is within ±3%.
5.Shrinkage rate of textile fabrics, weft skew.
The shrinkage rate of general fabrics is 3% weft 5%, individual high-stretch fabrics can be moderately relaxed to 8%, such as high-stretch fabrics with better slimming effect, it is not possible to require the shrinkage rate according to the standard of general fabrics. Weft skew indicates the distortion of the fabric, the general width of 165CM fabric, one meter length of the inner weft skew can not exceed 10CM, some products will be more demanding, special varieties of fabric factory must be done according to customer requirements.
6.The color fastness of the fabric.
Color fastness is affected by fiber raw materials and printing and dyeing process, even if the same fabric is the same dyeing and finishing process, the color fastness index of different colors is also very large. In general, black, navy blue, bright red, purple, green, etc., these are sensitive colors for color fastness, color fastness in similar products are very low, and even no matter how to do it can not meet the national standard and European and American standards, it will make fabric factories difficult to operate. Some individual customers will reduce the requirements for sensitive colors by half a level, and some brand companies with strong autonomy simply do not use dark colors, which avoids the trouble of low color fastness. The color fastness standards of textile fabrics are generally: 1 soap fastness 3-4; ② Wet rubbing fastness 2-3, dry rubbing 3-4; ③ perspiration fastness 3-4; ④ chlorine fastness 4-5; ⑤ Light fastness level 4; ⑥ Sublimation fastness 4.
7.Feel quality classification.
The feel of the fabric is more intuitive, in addition to the adjustment of printing and dyeing pretreatment, more rely on the improvement of finishing, the specific methods are: ① grinding; ② add softening; ③ Imitation tencel process, fiber opening and sand washing; ④ coating; ⑤ Firm finishing.
8.Color difference.
The color difference of the fabric, the international standard is more than 4. Including ① left and right color difference; Head and tail color difference; ③ cylinder difference.
9.PH value.
That is, PH, the pH value of general textile fabrics is required to be 4-7.5.
10.Loss.
Fabrics can not avoid loss when printing and dyeing, and the loss is also divided into normal loss and abnormal loss. Normal wear fabric factories are generally divided into printing and dyeing shrinkage, process differences and head and tail slightly. ① Printing and dyeing shrinkage is less than the amount of dyed finished products, this loss rate is due to the fabric category and printing and dyeing process changes, like cotton almost no dyeing shrinkage, polyester fabrics generally have 15%, and a variety of elastic fabric shrinkage can exceed 40%. ② Different processes, printing and dyeing shrinkage is also different, the general long car production shrinkage rate is small, cylinder production shrinkage rate is larger. ③ The head and tail problems can not be avoided, but the general impact is not large. The abnormal loss refers to the fabric to make a problem, this situation should be eliminated.
11.Special finishing of textile fabrics.
Special finishing can increase the function and use of textile fabrics, which are generally used by fabric factories. Generally, there are several items and indicators: ① three prevention, waterproof 90 points or more; ② oil and waterproof 5 or above; ③ Non-ironing grade 3.5; ④ UV resistant finish =50+; ⑤ Antistatic: charge surface density <5, friction charge density <7; ⑥ Acid and alkali prevention; ⑦ Stiff finishing; ⑧ easy decontamination finish 4; ⑨ Anti-pilling 4; Flame retardant: continuous burning time ≦2 seconds, flame retardant time ≦3 seconds, damage length ≦100.
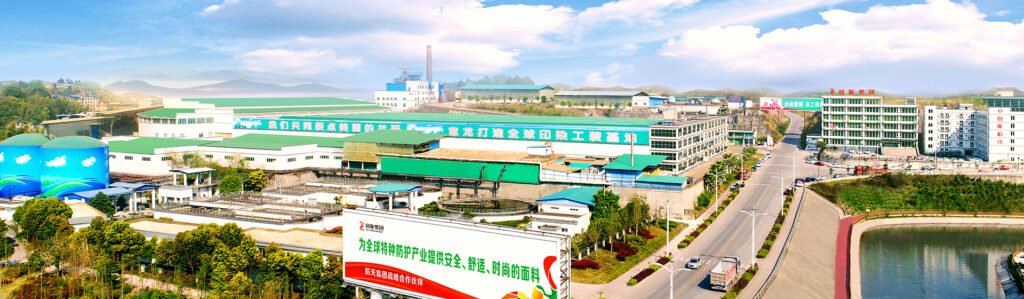
2. Dyeing process design
After receiving the sample from the customer, the first technical job is to review the sample. The main contents of sample examination are: raw material composition, fabric structure, color characteristics, product style and so on. Through sample review, understand the processing requirements of the fabric to be processed, so as to reasonably formulate the production process and ensure the smooth implementation of the process.
1.Check the raw material composition of the sample
Different types of dyes are selected for different fiber raw materials, different dyeing processes and processing methods, and different requirements for pre-dyeing and post-dyeing processes. For example, pure cotton fabrics need to be treated before scouring and bleaching to remove natural impurities, and in most cases need to be mercerized to ensure the evenness of dyeing. Therefore, the pre-dyeing process is long, the processing requirements are high, and the range of optional dyes is large, which is generally considered according to the requirements of color and fastness. The pure polyester fabric contains less impurities, the pre-treatment requirements are low, generally only need simple washing, the commonly used dye is disperse dye, and in order to avoid wrinkles in the fabric, it is generally appropriate to use open width processing. Therefore, through the review of the raw material composition of the sample, it helps us to rationally formulate the processing process of the product, accurately select the process method, and provide the necessary basis for the selection of dyes.
2. Check the color requirements of the samples
The same raw material products, if the color requirements are different, such as color, fastness, etc., the choice of dyes and processes are not the same. Such as pure cotton fabric bright red can be dyed with reactive dyes; Beige, light brown and other general use of VAT dye dyeing; Bright green if the fastness requirements are high, you can choose VAT dye dyeing, fastness requirements are general, you can choose reactive dye dyeing. It can be seen that the color requirements of samples are the most critical factors affecting the selection of product dyes and the formulation of processes.
3. Review the organizational structure of the sample
The fabric structure is different, the product style characteristics, color effect is different, dyeing and finishing processing methods are not exactly the same. Such as pure cotton line khaki body stiff, clear lines, soft luster, generally not suitable for rope processing, after finishing does not need to finish. And pure cotton horizontal satin smooth surface, bright luster, bright color, generally can be used rope processing, can also be used open width processing, but the use of rope processing should avoid fabric scratches, otherwise easy to cause uneven dyeing, and after finishing need to be calendered finishing. It is worth noting that the same dye, the same process on the same matrix material, if the product’s organization specifications are different, the dyeing effect is not exactly the same. The color and brightness of the general dye on the satin fabric is better than that of plain, twill, jacquard and suede fabric.
4. Review the style characteristics of the samples
Different styles of products choose different dyeing processes and processing methods. For example, the dyeing process of polyester/brocade interwoven products and two-color products is different, the former can choose monodisperse dyes, disperse/weakly acidic dyes, disperse/neutral dyes and other dyeing processes, the latter should choose disperse/neutral dyes dyeing process. Another example is the different styles of polyester-cotton blended products and polyester-viscose blended products, the former smooth, quite, cool, cotton products, the latter smooth, quite, waxy, wool-like products, so the general polyester-cotton blended fabric can be used tight processing, and polyester-viscose blended products are best used loose processing. It can be seen that only by fully understanding the style and requirements of the product can we reasonably develop the process and ensure product quality.
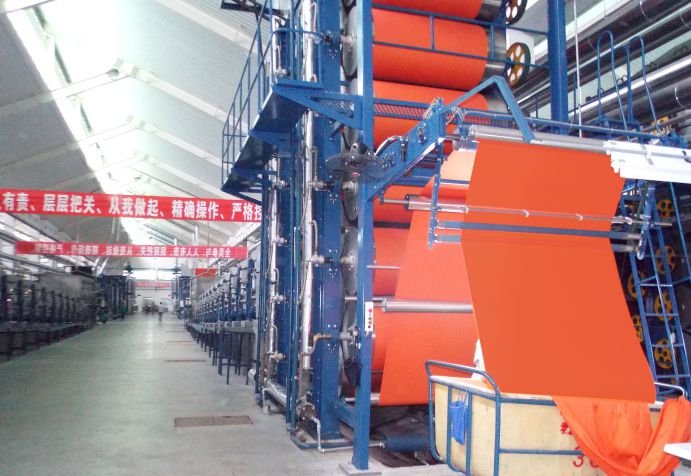
3.Read the depth of color. Medium. shallow
The shade of fabric color will affect the amount of final dye, will also affect the amount of auxiliaries during dyeing, and will affect the cost of dyeing, so how to distinguish the color shade?
To understand the shade of a color, you must first understand the properties of the color
Color has three important properties:
Hue (hue), saturation (purity) and lightness
So for dye dyeing, how do we determine the depth of the color?
It is generally determined according to the total amount of dye used, such as for immersion dyeing.
If the dye power fraction used is a conventional 100% dye, the total amount of dye (OWF) within 1% is called light, 1-2% is called dark, and more than 2% is called dark; (The above is a general classification, different companies will be slightly different)
There is also such a definition, if the color meter measures the L value obtained by the color sample, the L value is 50 to 70 for the medium color, more than 70 for the light color, and less than 50 for the dark color;
There is no clear definition of the color shade; Generally speaking, white, light rice, light yellow, etc., are light colors, and the total amount of dye below 0.5% must be light colors;
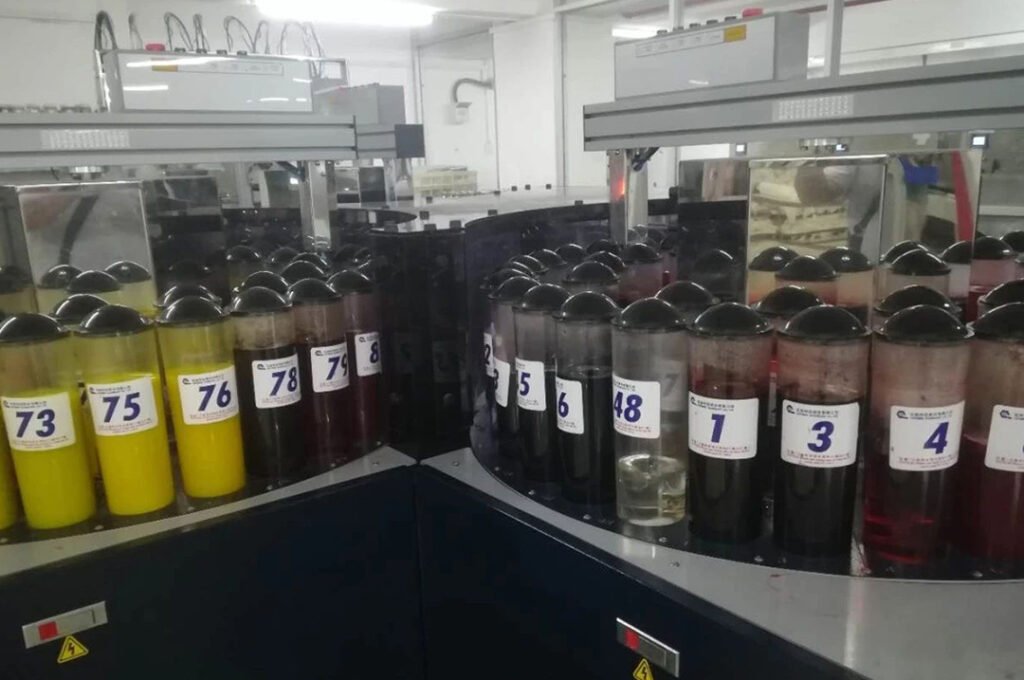
4. Dyeing bulk and sample control
In actual production, it is impossible to dye large and small samples completely without difference, and effective methods should be taken to correct it. Common solutions are summarized as follows:
1. Cleaning method
A. Wash with cold water
In cotton and its blended interwoven material, if the cotton component is dyed by direct dye or reactive dye, it appears floating color or dark color, which is generally washed further or washed with additives in water bath. If the water quality hardness is high, 0.5 ~ 2g/L chelating dispersant can be added to improve it.
B. Wash with warm water
When dyeing polyester blended interwoven material, there are many kinds of dyes and auxiliaries used, and it can be washed at 40℃ to facilitate the dissolution of the residue stained on the fabric. The cellulose fiber is dyed with direct blended dyes. If the overall color of the large sample is darker than that of the small sample, the color can be similar after washing with warm water, and the color fastness can be improved to a certain extent.
C. Hot water cleaning
Hot water cleaning is mostly used for silk or synthetic fibers and their interwoven materials dyed with acid, direct and alkaline dyes. If the color is too deep, it is necessary to remove 1 ~ 2 of the dye, and it can be washed in hot water at 70 ~ 80℃. 0.3 ~ 0.5 L of flat plus 0(levelling agent) can be added to the hot water bath of silk fabric. Polyester, nylon and other synthetic fiber blended interwoven material, can be added 0.5 to 1.0 L of repair agents or dyeing carriers. Due to the small amount of help added to the hot bath, the fabric only needs to be washed to room temperature with running water. If the dyed fabric is treated with cationic fixing agent and softener, it is best to add 2 to 4L dispersant DAM in the hot bath. Hot water washing (repair) is in principle carried out on the original dyeing equipment, such as nylon silk spinning, acetate fiber and its interwoven silk after dyeing, if the overflow machine (rope) hot water washing, will cause the fabric to produce permanent wrinkles.
In actual production, it is impossible to dye large and small samples completely without difference, and effective methods should be taken to correct it. Common solutions are summarized as follows:
1. Cleaning method
A. Wash with cold water
In cotton and its blended interwoven material, if the cotton component is dyed by direct dye or reactive dye, it appears floating color or dark color, which is generally washed further or washed with additives in water bath. If the water quality hardness is high, 0.5 ~ 2g/L chelating dispersant can be added to improve it.
B. Wash with warm water
When dyeing polyester blended interwoven material, there are many kinds of dyes and auxiliaries used, and it can be washed at 40℃ to facilitate the dissolution of the residue stained on the fabric. The cellulose fiber is dyed with direct blended dyes. If the overall color of the large sample is darker than that of the small sample, the color can be similar after washing with warm water, and the color fastness can be improved to a certain extent.
C. Hot water cleaninHot water cleaning is mostly used for silk or synthetic fibers and their interwoven materials dyed with acid, direct and alkaline dyes. If the color is too deep, it is necessary to remove 1 ~ 2 of the dye, and it can be washed in hot water at 70 ~ 80℃. 0.3 ~ 0.5 L of flat plus 0(levelling agent) can be added to the hot water bath of silk fabric. Polyester, nylon and other synthetic fiber blended interwoven material, can be added 0.5 to 1.0 L of repair agents or dyeing carriers. Due to the small amount of help added to the hot bath, the fabric only needs to be washed to room temperature with running water. If the dyed fabric is treated with cationic fixing agent and softener, it is best to add 2 to 4L dispersant DAM in the hot bath. Hot water washing (repair) is in principle carried out on the original dyeing equipment, such as nylon silk spinning, acetate fiber and its interwoven silk after dyeing, if the overflow machine (rope) hot water washing, will cause the fabric to produce permanent wrinkles. 2. Additive method
A. Add electrolytes
(1) Using direct dyes to dye cellulose fibers, dyeing large sample depth is often not enough. If there is still dye in the dyeing bath, 1.5-5.OG/L electrolyte (NaCl, Na2SO4) can be added to promote dyeing. This is very effective for direct salt effect dyes such as direct fast yellow 3RLL, orange (L, bright Red BNL, Red 4BL, Ruby RNLL, Purple BL, Blue BL, B2RL, Sky Blue G, Turquoise Blue GL, green 5GLL, green GL, grey 4GL, grey GB, etc. For direct dyes with temperature effects, a certain temperature needs to be maintained.
(2) Dyeing protein fibers with acid dyes, or dyeing acrylic fibers with basic dyes or cationic dyes, dyeing large samples with too deep color or color flowers, you can add 3 ~ 6g/L Na2SO4 to fade or even dye.
B. Add acetic acid
(1) Use acid dyes to dye silk, wool and other protein fibers, such as the dye sample is light and there is still color in the dye solution, you can add O.5-2ml/L of 98% acetic acid to promote dyeing. Before adding, the steam valve must be closed, diluted with 10 times cold water, and added slowly while the dye is running to avoid causing new color flowers.
(2) Dye cellulose fibers with K and KN reactive dyes, if the large sample is deep, you can add 2-3mL/L of 98% acetic acid, treat 3Omin at 90-95 ℃, and promote the dye part to break the bond and eliminate color, generally about 20% lighter.
(3) When dyeing silk with basic dyes or acrylic fibers with cationic dyes, if the large sample is too deep, 2 ~ 3mI/L acetic acid can be used to treat 2O ~ 30min in a warm bath at 4JD and 60℃, so that the dyes can be dissolved and reduced by 20% ~ 30%.
C. Add levelling agent
(1) When disperse dyes are used to dye polyester and its blended interwoven material, the large sample is darker than the small sample, high temperature levelling agent or repair agent can generally be added. Large color light, should add the corresponding dye, but should pay attention to the addition to close the steam valve, to avoid the production of color flowers, first add the appropriate amount of levelling agent. In addition, when additional dyeing of disperse dyes, it is necessary to heat up to a certain dyeing temperature, and hold heat for 15-20min, and then cool down and reduce pressure and sample.
(2) When dyeing cellulose fibers, silk, wool and nylon fabrics with direct, acidic, neutral and other dyes, in principle, flat plus O can be used to remove migrating dyes to achieve even dyeing. The amount of O on wool fabrics generally cannot exceed 0.3g/L. In order to prevent felting of sheep, wool protection agent Seropo WOK2% 1% (DYS-tar) can also be added. When dyeing nylon with neutral dyes, if the color is too deep or there is a rung to cover, the use of color Lego N-ER3% ~ 5% (D’ystar) effect is excellent.
(3) When dyeing acrylic fiber, alkali-modified polyester and silk with alkaline and cationic dyes, if the color of the dyed large sample is slightly darker, it can be cleaned with hot water; If the color of the large sample is about 20% deep, 2 ~ 4L surfactant 1227 can be added when the dyeing residue is basically washed out, and the fading can be achieved through the competitive effect.
D. Add whitener
When dyeing ruby, rose, violet blue, azure blue and brilliant violet and other bright colors, if you feel that the large size is not bright enough, you can generally add 0.0015% ~ 0.0025% (owf) fluorescent whitening agent, the lighter the color, the less the amount. The effect of fluorescent whitening agent 4BK on cotton textile is better, which has weak fluorescence, strong brightness, less amount, good adjustability, and wide color adaptation, and is not easy to “jump light”. The “jump light” caused by fluorescent whitening agent can be removed by fluorescent stain remover that does not affect the color brightness.\
E. Add dye carrier
For polyester cotton (viscose) and cotton (viscose), because polyester and cotton are hydrophobic fibers, their color is deeper than cotton and viscose hydrophilic fibers, you can add 2-4 mL/L dyeing carrier in 60℃ clear water bath, and then gradually heat up to 80 ~ 9O℃, so that the dye on the hydrophobic fiber slowly desorbed down, to achieve the two phase color light consistency. It has been proved that the dyeing carrier can not only dissolve disperse dyes on hydrophobic fibers, but also dissolve other dyes. When the temperature rises to 80 ° C, the operator should constantly sample the sample, and the general insulation is consistent with the large sample.
3. Dye (face) material addition method
A. When adding disperse dyes to polyester for color correction, it is best to first reduce the dyeing bath temperature to below 80℃, then fully dilute the dissolved dyes in advance, and add them within 5 ~ 8min, and then continue to rise the temperature to the original dyeing temperature, and heat preservation dyeing above 15rnin to ensure uniform color before and after dyeing, in order to reduce the influence on thermal setting.
B. If the color difference between large and small samples is found after the dye is out of the tank, you can add dye or adjust the color light on the large sample. When adjusting, in addition to calculating the variety and quantity of dyes required on the sample, 15% to 20% of the original prescription dyes should also be added in the blank bath.
C. For the color of 3 to 4 kinds of dyes, such as rice gray, tile gray, incense gray, silver gray and ivory white, can not be used to repair the color difference between large and small samples.
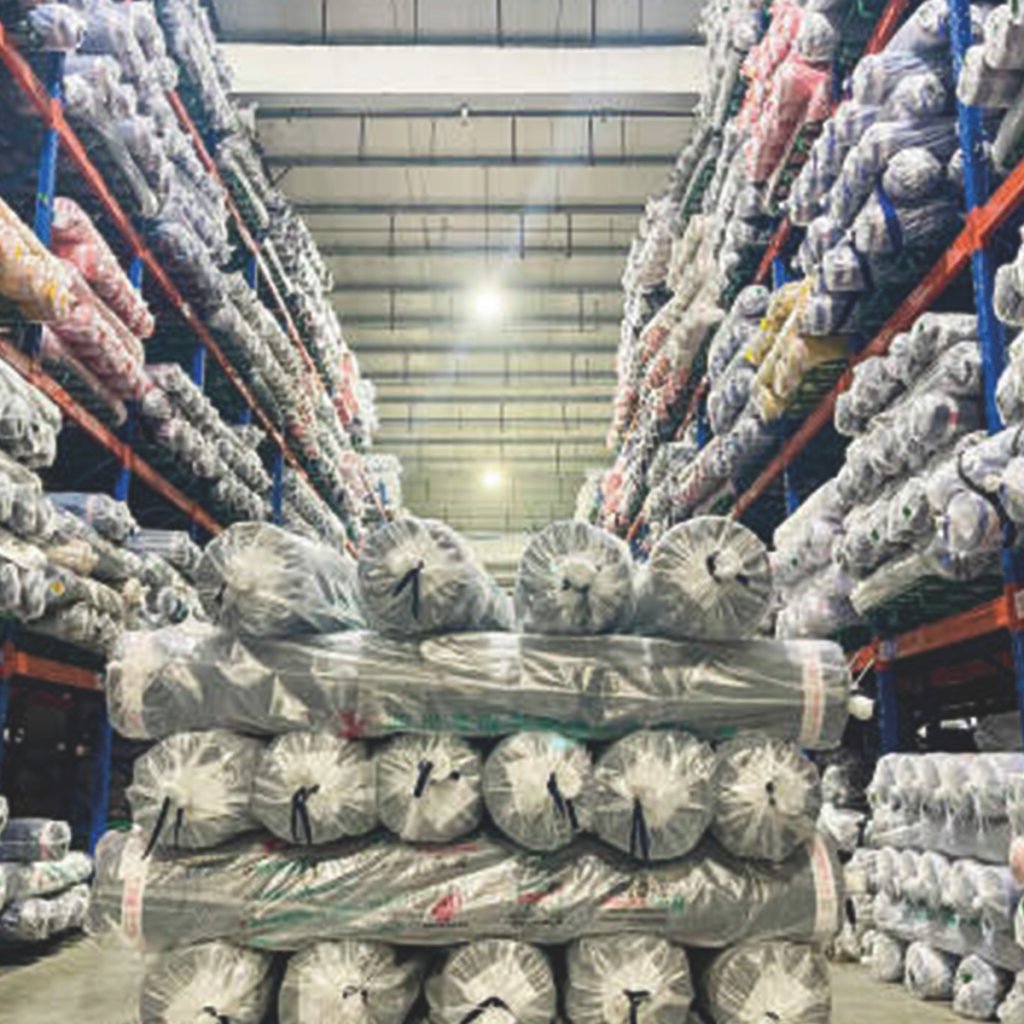