Traditionally, cloth is woven by a shuttle driving the weft yarn back and forth through the warp yarn. Generally, there are obvious edge structures on both sides, and both gray and finished fabrics are flat. The gray fabric of knitted fabrics is often cylindrical, and the finished product becomes flat after being opened and shaped.

The concept of yarn count density
Fabrics vary widely, how to express different specifications? Yarn count density is an important indicator.
Yarn count: Generally speaking, the British count is the one we come into contact with. The specific definition is: the calculation of the British count of cotton yarn: the number of 840 yards of cotton yarn with a common weight of one pound is called the British count. For example: if it contains 32 840 yards, it is called 32 British counts, and so on. The higher the count, the thinner the yarn. The British branch is generally represented by s.
At the same time, there is also an indicator of Daniel to indicate the thickness of the fiber. It is the opposite of the British branch. The higher the fiber, the thicker the fiber. The specific definition is: fixed length 9000 m, weight 1 g = 1 D. If a fiber 9000 meters long weighs 70 grams, Then it is 70D. Converted to British currency it is 76s
Daniel is generally used to describe finer fibers, such as nylon, polyester, spandex, etc.
Density: The number of warp and weft threads per inch is called density. We have a density mirror, the size of the box is 1″, the density is determined by counting the number of rods.
For example: 20×16/128×60, which means that the warp yarn is 20s, the weft yarn is 16s, there are 128 warp yarns and 68 weft yarns per inch. This is just the most basic fabric. There are also many more complex fabrics, and the method of expressing yarn count is correspondingly more complicated.
Generally speaking, the density of non-elastic fabrics refers to the yarn count density of the gray fabric, and the density of the finished product will change accordingly. The width of the gray fabric of most non-elastic fabrics is 47” or 63”, and their finished width is 44” or 58” respectively. Taking 128×60/20×16 as an example, 47” x 128/44”=136. So this fabric The finished product’s warp density should be around 136. The density of weft yarns basically does not change before and after the finished product, with a maximum of 1-2 yarns.
Gray fabric will lose some weight after being processed layer by layer during the dyeing and finishing process, so the yarn count of the finished product will be 1-2 counts thinner than the yarn count of the gray fabric.
Concepts of various organizational structures
In addition to the yarn count density, there is another important indicator to understand what the cloth looks like, and that is the organizational structure of the cloth. Generally speaking, there are mainly the following categories:
1. Plain weave fabric, the warp and weft yarns are interwoven one up and down, which is the most basic weaving method. The thinner and lighter plain weave fabric is called poplin, and the thicker and lighter plain weave fabric is called canvas.
2. There are three common types of twill fabrics, 2/1, 3/1, and 2/2. The numbers up and down refer to the ups and downs of the warp yarns. 3/1 means that the warp thread floats on top of 3 weft threads, then sinks under one weft thread, and then floats on top of 3 weft threads. This kind of fabric is called yarn card or thread card.
3. For satin fabrics, it is generally 4/1, but also 5/3. This is more complicated, as long as you understand that the surface of this kind of fabric has a strong luster. There are more direct tributes.
4. Jacquard type: It is completed by a more complex dobby loom, usually with small jacquards, which is called dobby. Such as squares, wick strips, herringbone and satin strips, all are small jacquards.
5. Velvet plants mainly include corduroy and velveteen. The main characteristic of corduroy is that the weft density is much higher than the warp density. Because the weft yarn becomes velvet yarn after being opened.
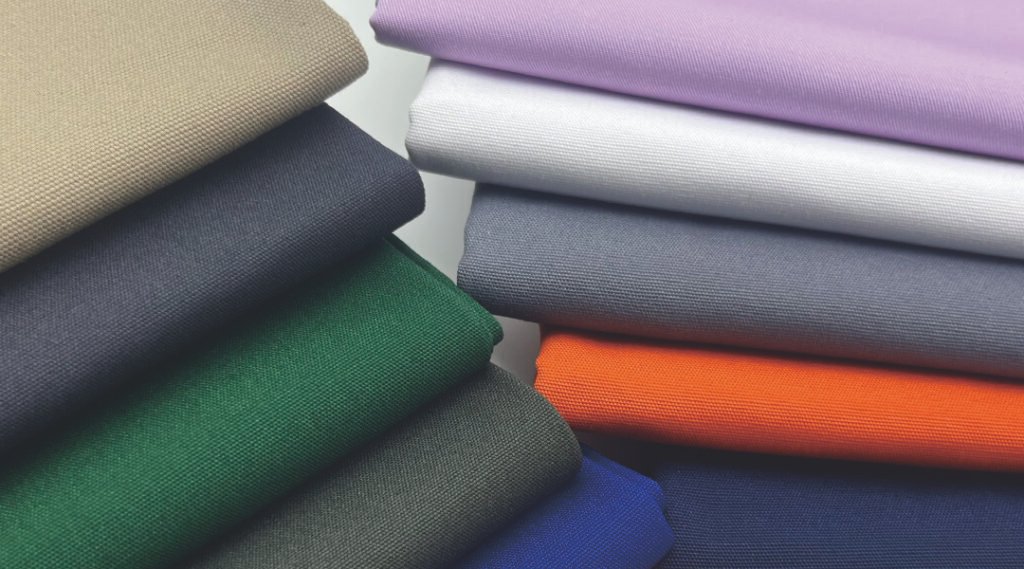
Different dyeing and finishing methods
Generally speaking, there are two methods of dyeing and finishing woven fabrics, one is dyeing and the other is yarn-dyed.
Dyeing refers to weaving the gray fabric first and then sending it to the dyeing factory. After desizing, singeing, scouring, mercerizing, (sanding) dyeing, shaping, pre-shrinking, softening and other processes, the colored fabric is obtained. Most of the printing processes are the same, mainly changing the dyeing process into printing.
Dyeing is also divided into two types: long car continuous dyeing and vat dyeing.
Yarn-dyed weaving refers to dyeing the yarn first and then warping, sizing, weaving, and finishing to obtain the finished fabric. Yarn-dyed fabrics are mainly in plaid and striped patterns.
The difference between various dyes
There are basically four types of dyes, the most important ones are reactive dyed (also known as reactive dyes) and vat dyed (also known as reducing dyes). Among them, Shilin’s color fastness is the best. But one thing is very important. One dye cannot cover all the color spectrum. Some colors can only be made with one dye, such as navy blue, which can only be made with reactive dyes. Shilin’s color spectrum is mainly medium and light colors.
There is also a kind of paint, which fades badly after being washed. It is often used by customers who want an old look after being washed. Color fastness is very poor before washing, but fair after washing.
There are also sulfur dyes, which have been basically eliminated and are used to make corduroy black. They have poor color fastness and have a strong corrosive effect on cotton fibers. The tear strength is very poor over time.
Several main test indicators
Divided into two categories: physical indicators and color fastness
Physical indicators include: yarn count density, weight, tensile strength, tear strength, PH, shrinkage, composition, flame retardancy, etc.
Color fastness includes: washing fading, staining, friction, light, chlorine bleaching, non-chlorine bleaching, actual washing discoloration, etc.
Price composition
Dyeing printed fabrics: gray fabric price + dyed and finished finished product price. The gray fabric price consists of the yarn raw material cost plus the weaving labor cost.
Yarn-dyed fabric: yarn raw material price + dyeing cost + weaving labor cost + finishing cost
